Porosity in Welding: Identifying Common Issues and Implementing Best Practices for Avoidance
Porosity in welding is a prevalent issue that frequently goes unnoticed up until it creates considerable troubles with the stability of welds. This common issue can compromise the strength and longevity of welded structures, posing safety threats and resulting in pricey rework. By understanding the source of porosity and implementing efficient prevention techniques, welders can dramatically boost the top quality and reliability of their welds. In this discussion, we will certainly explore the key aspects contributing to porosity development, examine its damaging results on weld performance, and review the very best practices that can be adopted to minimize porosity incident in welding processes.
Usual Sources Of Porosity

Utilizing dirty or damp filler products can present pollutants right into the weld, contributing to porosity concerns. To minimize these typical causes of porosity, comprehensive cleansing of base metals, correct securing gas selection, and adherence to optimal welding specifications are vital techniques in accomplishing top notch, porosity-free welds.
Influence of Porosity on Weld Top Quality

The existence of porosity in welding can substantially compromise the architectural integrity and mechanical homes of welded joints. Porosity produces voids within the weld metal, compromising its overall stamina and load-bearing capacity.
Among the main consequences of porosity is a decline in the weld's ductility and sturdiness. Welds with high porosity degrees tend to display lower effect stamina and minimized ability to flaw plastically before fracturing. This can be especially worrying in applications where the bonded elements are subjected to vibrant or cyclic blog loading problems. Porosity can impede the weld's ability to properly transfer forces, leading to premature weld failure and possible security risks in important frameworks. What is Porosity.
Best Practices for Porosity Prevention
To improve the architectural honesty and high quality of bonded joints, what particular steps can be carried out to lessen the incident of porosity during the welding procedure? Using the right welding method for the certain material being bonded, such as changing the welding angle and weapon setting, can better avoid porosity. Routine inspection of welds and immediate remediation of any type of you could look here issues recognized throughout the welding process are crucial techniques to avoid porosity and generate high-grade welds.
Relevance of Correct Welding Techniques
Applying correct welding techniques is critical in making sure the structural integrity and quality of bonded joints, building on the structure of effective porosity avoidance steps. Welding techniques straight influence the overall toughness and sturdiness of the welded framework. One key element of appropriate welding techniques is click to find out more preserving the correct warm input. Extreme heat can cause boosted porosity as a result of the entrapment of gases in the weld swimming pool. Alternatively, not enough warmth may lead to insufficient fusion, developing possible weak points in the joint. Furthermore, using the suitable welding specifications, such as voltage, present, and travel speed, is critical for achieving sound welds with minimal porosity.
In addition, the option of welding process, whether it be MIG, TIG, or stick welding, need to align with the specific demands of the project to make certain ideal outcomes. Appropriate cleansing and prep work of the base steel, along with choosing the best filler product, are also crucial elements of skilled welding techniques. By sticking to these finest practices, welders can reduce the risk of porosity formation and generate top quality, structurally audio welds.
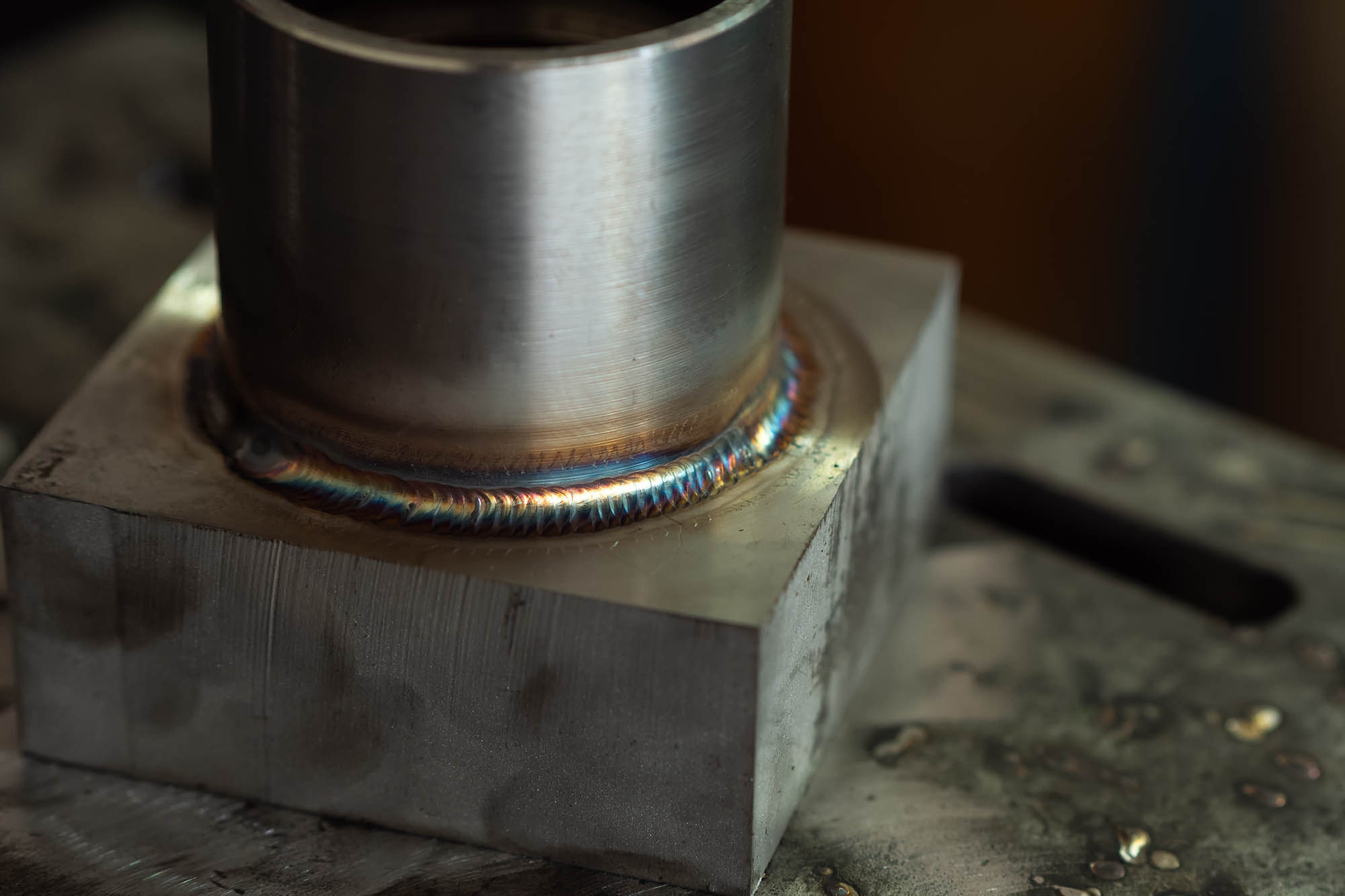
Examining and Quality Assurance Procedures
Quality control actions play an important duty in verifying the stability and dependability of bonded joints. Evaluating treatments are vital to find and prevent porosity in welding, ensuring the strength and resilience of the end product. Non-destructive testing techniques such as ultrasonic testing, radiographic screening, and aesthetic evaluation are commonly employed to recognize possible problems like porosity. These strategies permit the evaluation of weld high quality without compromising the integrity of the joint. What is Porosity.
Post-weld inspections, on the other hand, evaluate the final weld for any kind of problems, including porosity, and verify that it satisfies specified criteria. Carrying out a detailed top quality control plan that includes thorough screening treatments and inspections is extremely important to lowering porosity issues and making sure the total high quality of welded joints.
Conclusion
Finally, porosity in welding can be a common problem that affects the high quality of welds. By recognizing the typical reasons for porosity and carrying out best practices for prevention, such as correct welding strategies and screening procedures, welders can guarantee high top quality and trustworthy welds. It is necessary to prioritize prevention techniques to decrease the occurrence of porosity and maintain the stability of welded frameworks.